Research Projects
Current Projects
Performance Optimization of the Automotive Cooling System using Nanofluids
The project focuses on enhancing the thermal efficiency of automotive cooling systems through the integration of advanced heat transfer fluids and intelligent predictive models. By incorporating nanofluids—engineered colloidal suspensions of nanoparticles within conventional coolants—the study aims to significantly improve heat dissipation and cooling performance. Experimental and computational investigations are conducted to evaluate the thermo-physical behavior of various nanofluid formulations under dynamic engine conditions. In parallel, machine learning algorithms are developed to model, analyze, and optimize system performance by correlating input variables (e.g., nanofluid concentration, flow rate, temperature) with key output metrics such as heat transfer rate and pressure drop. This multidisciplinary approach is expected to provide actionable insights for the design of next-generation, energy-efficient automotive cooling systems.
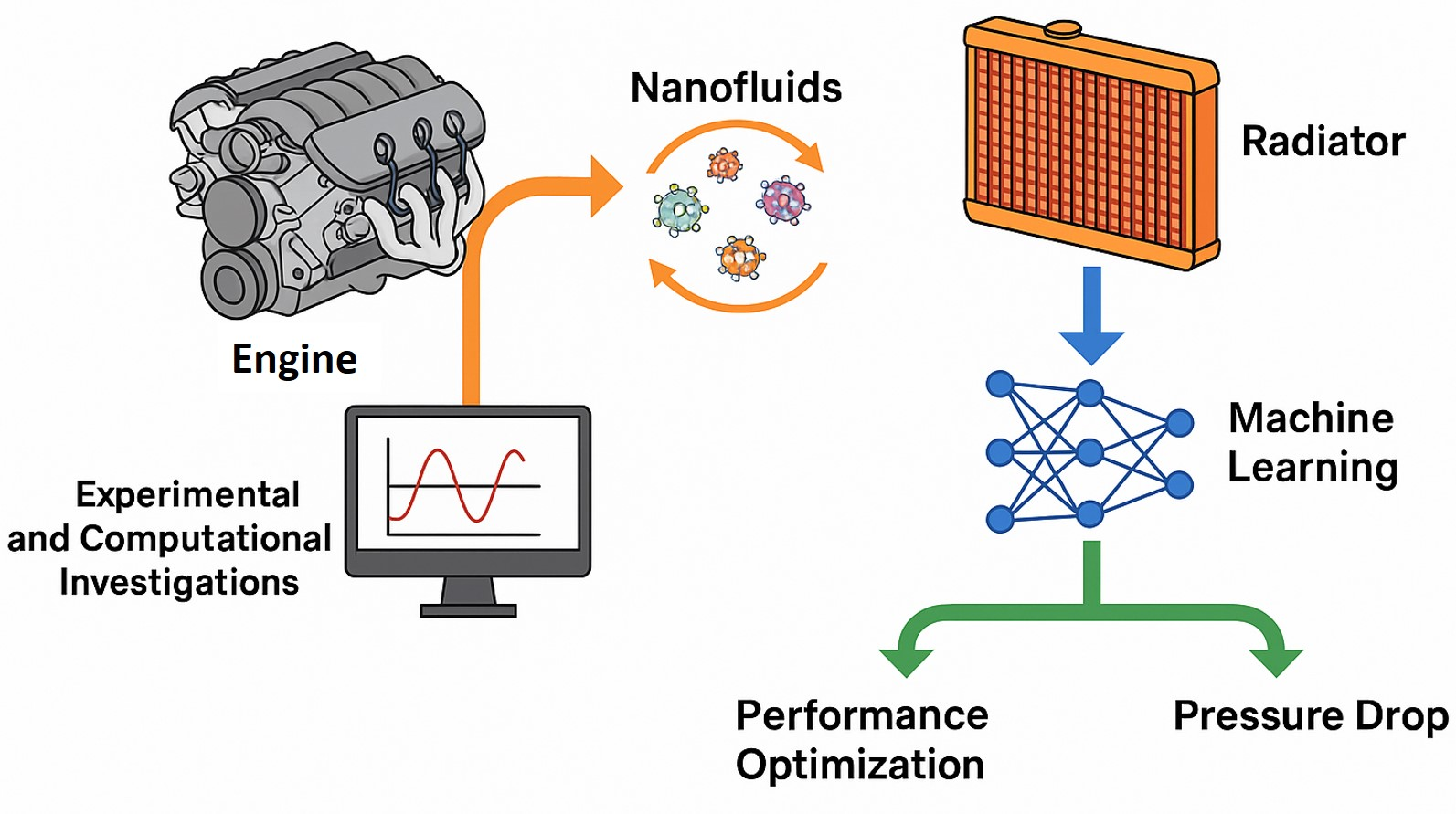

Developing a Smart Digital Twin Framework for Forecasting HAZ and Isotherms in High-Frequency Induction Pipe Welding
Induction pipe welding utilizes high-frequency electromagnetic induction to heat the pipe edges, enabling their fusion without physical contact or the use of filler material. This project focuses on developing a digital twin framework for the induction welding process by integrating physics-based simulations with machine learning models to enable real-time monitoring, prediction, and feedback control. The proposed approach aims to accurately forecast the extent of the heat-affected zone (HAZ) prior to actual welding. Ultimately, a generalized tool will be created to compute both the HAZ and transient temperature isotherms, allowing process optimization before executing real-time welding operations.Results from the numerical simulation: We have developed a numerical model of the induction welding process as part of our efforts to build a digital twin framework, which integrates machine learning techniques for enhanced prediction and control.
Machine Learning-Driven Real-Time Control of Melt Pool and HAZ in Wire Arc Additive Manufacturing (WAAM)
Live control of the Wire Arc Additive Manufacturing (WAAM) process is a rapidly evolving research area with significant industrial relevance. This project aims to improve the quality and precision of WAAM by leveraging supervised machine learning models—such as Random Forest, Support Vector Machines (SVM), and Neural Networks—to enable real-time prediction and control of melt pool dimensions and the heat-affected zone (HAZ). By developing data-driven control algorithms for melt pool regulation, the project seeks to enhance the geometrical fidelity and mechanical performance of WAAM-produced components. Ultimately, this work supports the implementation of adaptive control systems in WAAM for high-performance metal part fabrication in sectors like aerospace, automotive, and energy.
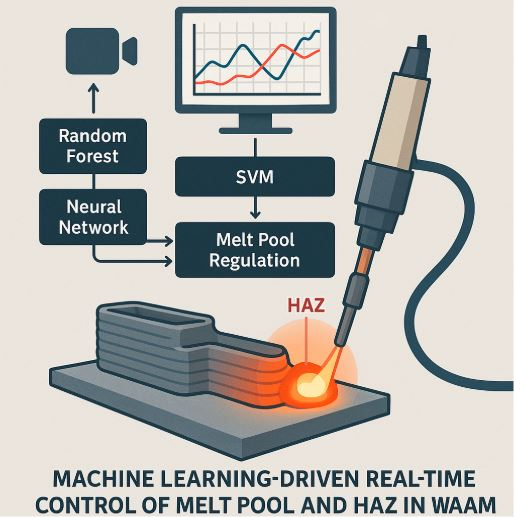
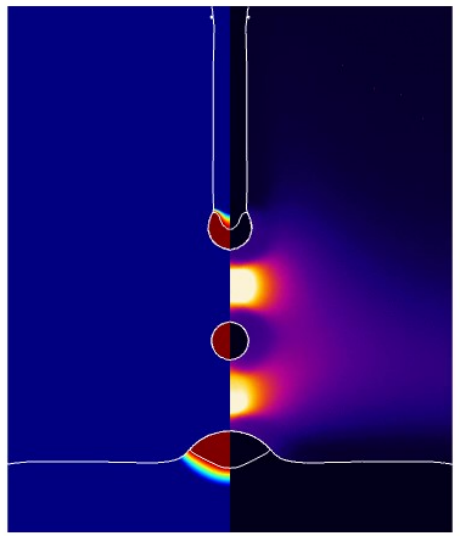
Unified Multi-Physics and AI-Driven Predictive Control Framework for WAAM
This project aims to develop a comprehensive multi-physics simulation model that captures the complex, interrelated phenomena of droplet formation, arc plasma behavior, and melt pool dynamics in Wire Arc Additive Manufacturing (WAAM). By integrating thermal, fluid, and electromagnetic physics into a unified computational framework, the model will offer a high-fidelity representation of the WAAM process. It will enable accurate prediction of droplet transfer behavior under varying arc and wire feed conditions, simulation of arc dynamics including energy distribution and electromagnetic forces, and detailed tracking of melt pool evolution involving temperature gradients, fluid flow, and solidification. The simulation output will be used to train a machine learning-based surrogate model, facilitating real-time predictive control for smart WAAM systems. This approach will support adaptive process optimization by identifying critical parameters that influence build quality, ultimately minimizing defects, and improving the performance and consistency of WAAM-fabricated components for advanced manufacturing applications.
Numerical Investigation of Heat Transfer Enhancement in Microchannels with Backward Trapezoidal Grooves
This project investigates the impact of geometric design parameters on the thermo-hydraulic performance of microchannel heat sinks featuring backward right-angled trapezoidal grooves along the sidewalls. The objective is to optimize heat transfer efficiency and pressure drop by examining how variations in channel width (Wc), spacing between groove leading edges (Sr), and forward angle (θ) affect fluid flow and thermal behavior within the microchannels. To achieve this, Computational Fluid Dynamics (CFD) simulations are conducted in ANSYS Fluent, following the Taguchi Design of Experiments (DoE) methodology using an L9 orthogonal array. Key performance indicators such as pressure drop (ΔP) and wall temperature (Tw) are analyzed across different configurations. The findings offer valuable guidance for the design of compact, high-performance thermal management systems applicable to electronics cooling, lab-on-chip platforms, and microscale energy technologies.
(a) Design parameters of TB-MC groove (b) Schematic diagram and computational domain of TB-MC with dimensions (mm)

Past Projects
Developing a Numerical Model of Arc, Metal Transfer and its Impingement on Weld Pool in Variable Polarity Gas Metal Arc Welding (VP-GMAW)
This research project involves the development of a comprehensive numerical model to simulate the complex physical phenomena occurring during Variable Polarity Gas Metal Arc Welding (VP-GMAW). Using COMSOL Multiphysics, the study captures the coupled behavior of the arc plasma, metal droplet transfer, and its interaction with the weld pool under the influence of alternating current polarity. The model accounts for electromagnetic forces, fluid dynamics, heat transfer, and phase change, enabling a realistic simulation of arc behavior and droplet impingement. A key focus of the project is to investigate how polarity switching affects arc characteristics, droplet trajectories, and the resultant flow and temperature fields in the molten pool. The findings provide critical insights into the dynamic response of the welding process to polarity changes and contribute to the advancement of VP-GMAW techniques for improved weld quality, reduced spatter, and controlled heat input—making it valuable for high-performance and precision welding applications.
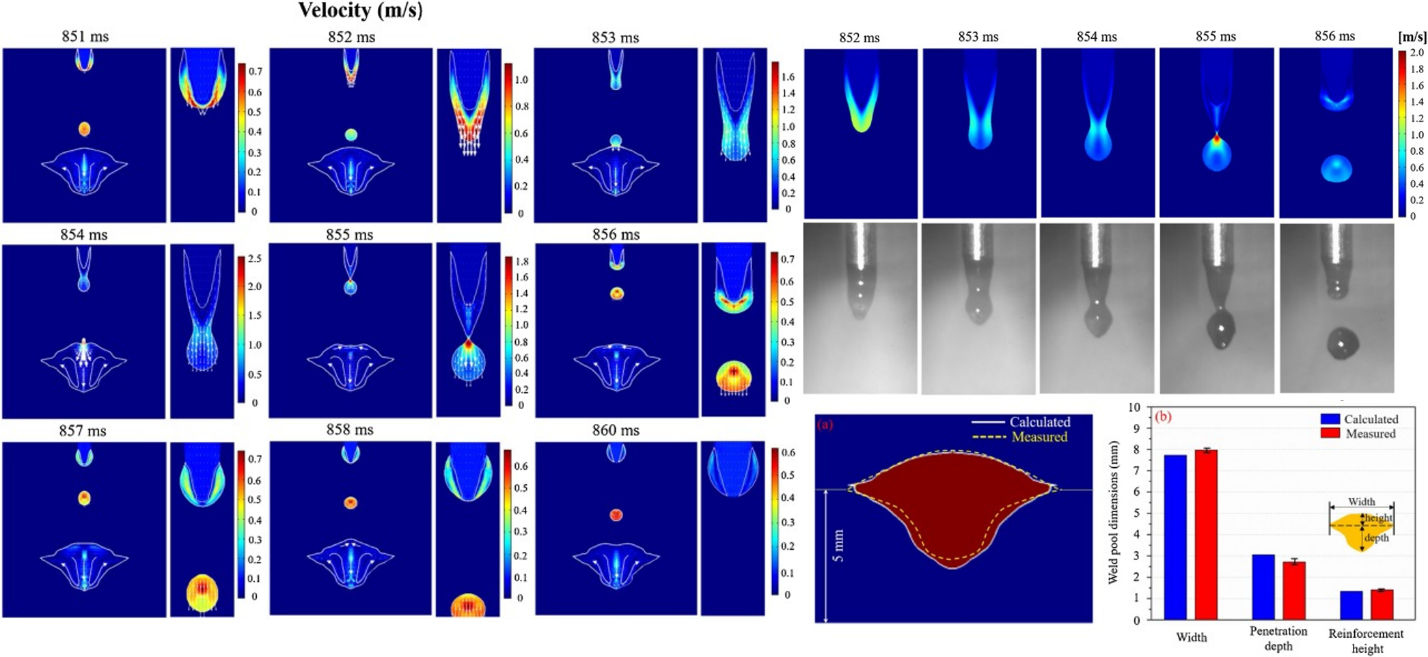
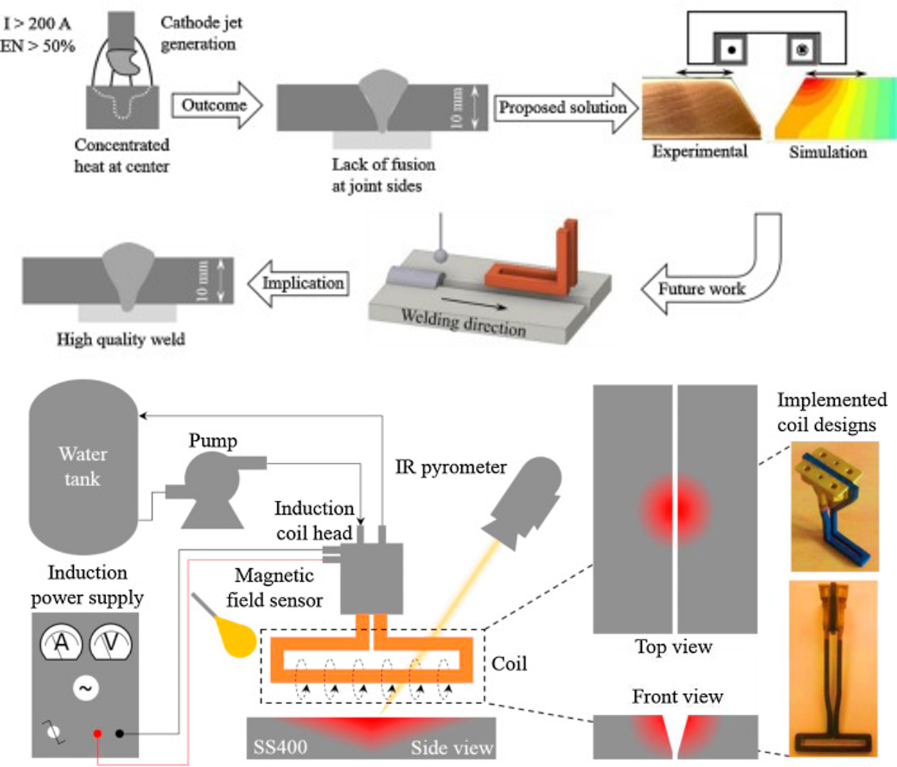
Design and Integration of Induction Heating in AC-GMAW in Thick Steel Plate Welding
This research project centers on developing and optimizing an induction heating system to support alternating current gas metal arc welding (AC-GMAW) processes. The work involves the design and electromagnetic-thermal simulation of an induction coil integrated with the welding torch to preheat the base material, thereby improving arc stability, fusion characteristics, and overall weld quality. Using a physics-based modeling approach validated by experimental trials, the project evaluates how parameters such as coil geometry, positioning, and excitation frequency affect the heat distribution in the workpiece. This research aims to enhance the energy efficiency and precision of hybrid welding systems, contributing significantly to advanced manufacturing practices and paving the way for intelligent control strategies in digital twin frameworks.
Microstructural and Mechanical Characterization of AC-GMAW Welds Under Varying EN Ratios and Current Levels
This research project focuses on investigating the influence of electrode negative (EN) ratio and welding current on the microstructural evolution and mechanical performance of welds produced by alternating current gas metal arc welding (AC-GMAW) on square groove butt joints. By systematically varying the EN ratio and current levels, the project aims to understand their effects on heat input, penetration profile, grain structure, and resulting mechanical properties such as tensile strength and hardness. The findings from this study provide critical insights into optimizing AC-GMAW parameters to achieve improved weld quality and structural integrity, especially in applications involving thick-section materials where precise thermal control and joint strength are essential.
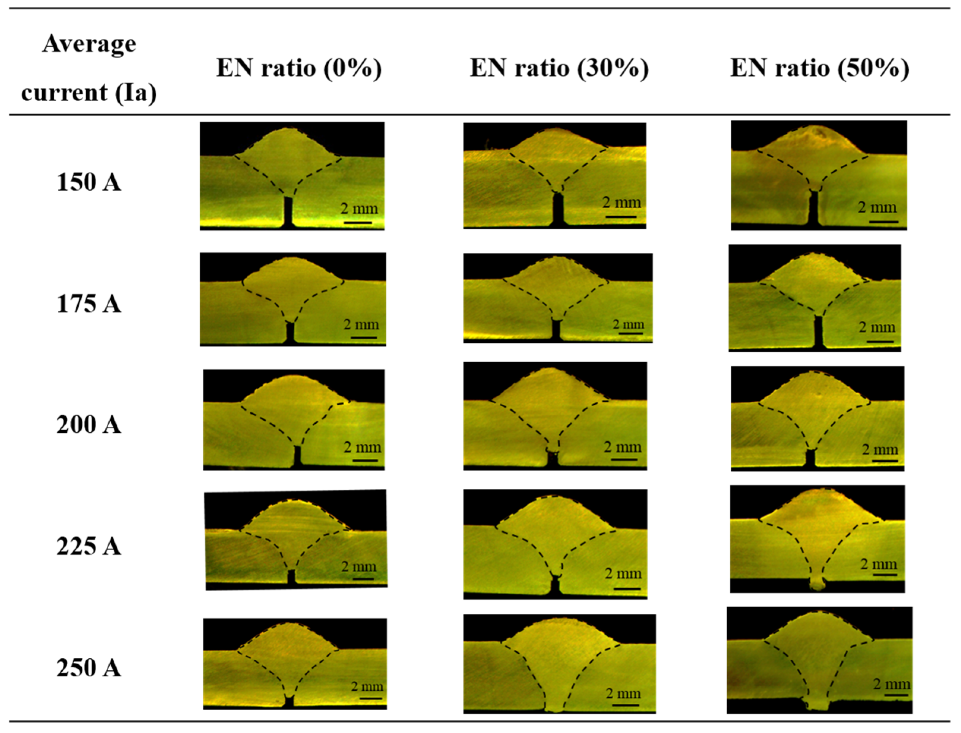
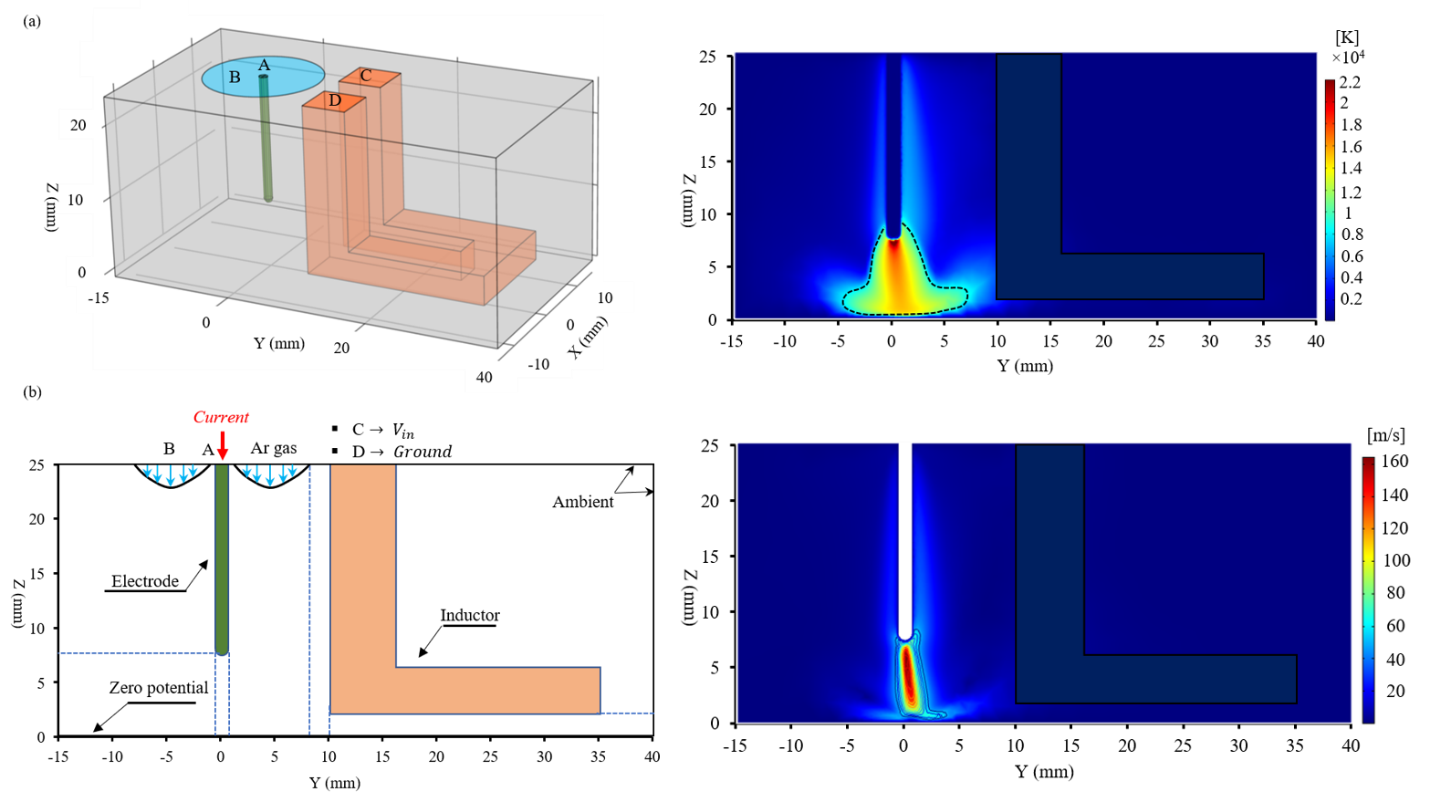
Numerical Investigation of Arc Stability in Induction Heating-Assisted GMAW
This research project focuses on understanding and modeling the complex interaction between induction heating and the gas metal arc welding (GMAW) process, particularly the phenomenon of arc interruption. By integrating a numerical approach, the study simulates the thermal and electromagnetic fields involved in the hybrid welding process to analyze how induction heating influences arc stability, metal transfer, and overall weld quality. The project aims to provide critical insights into the mechanisms leading to arc interruption and to identify optimal process parameters that can enhance arc stability and improve welding efficiency. This work contributes to advancing hybrid welding technologies for industrial applications by supporting more reliable and controlled welding processes.
AC-GMAW for Thick AH36 Steel Welding
This research project investigated the feasibility of using Alternating Current Gas Metal Arc Welding (AC-GMAW) for single-pass welding of thick AH36 steel plates (6 mm to 8 mm) in a square groove butt joint configuration. The study aimed to optimize welding parameters, including travel speed and joint gap, to achieve deep penetration, sound weld quality, and efficient gap bridging. Experimental results demonstrated that maintaining a 2 mm joint gap and specific welding speeds (e.g., 12–14 mm/s for 6 mm plates) yielded optimal outcomes, including complete penetration and minimal heat-affected zone (HAZ). Microstructure analysis revealed fine grain distribution in the weld metal, while hardness and tensile tests confirmed the mechanical integrity of the joints, though ductility decreased compared to the base metal. The findings provide practical guidelines for industrial applications, particularly in shipbuilding, where AH36 steel is widely used. The project highlights AC-GMAW as a cost-effective alternative to traditional methods, offering high deposition rates and reduced heat input.
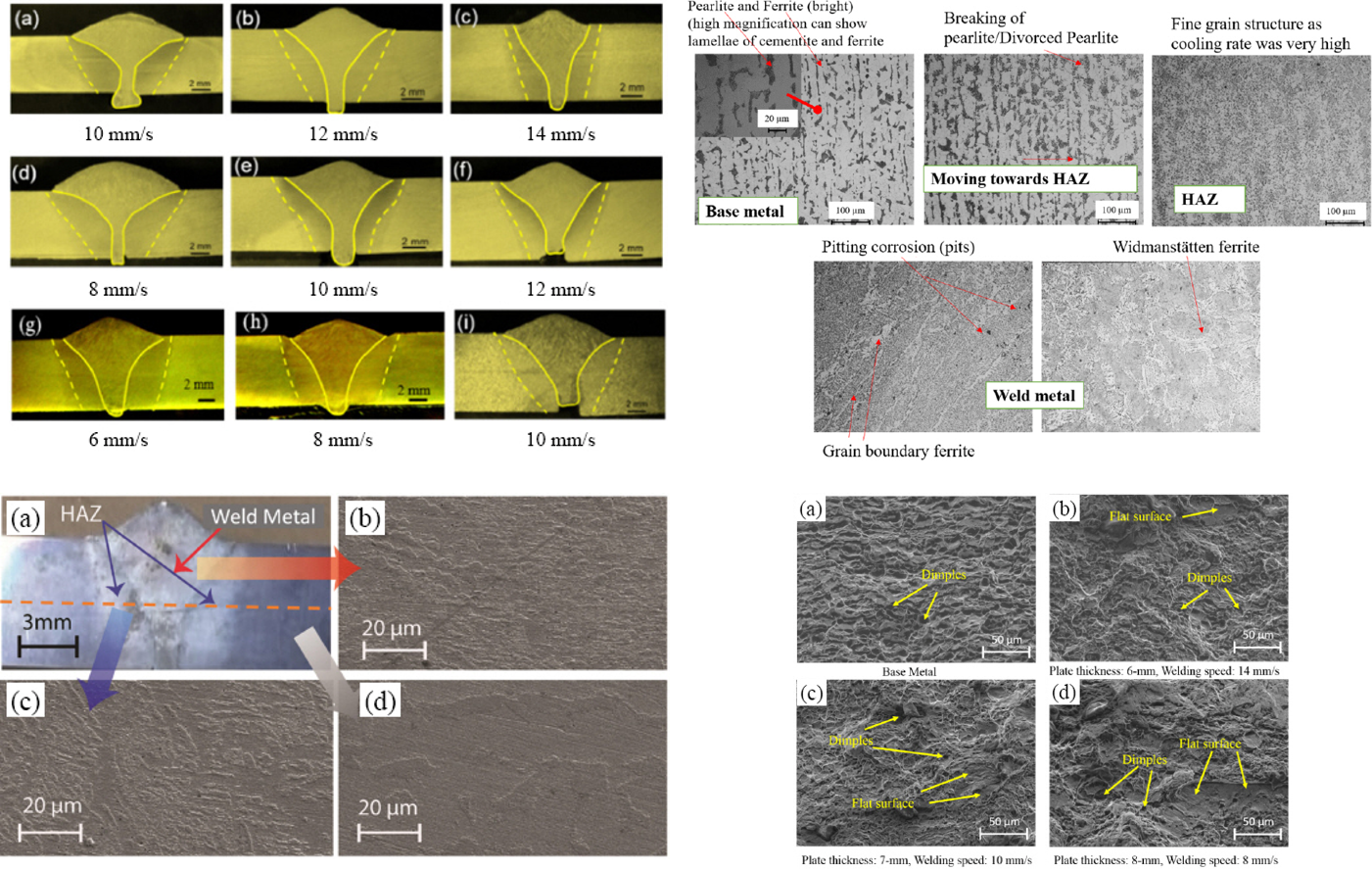
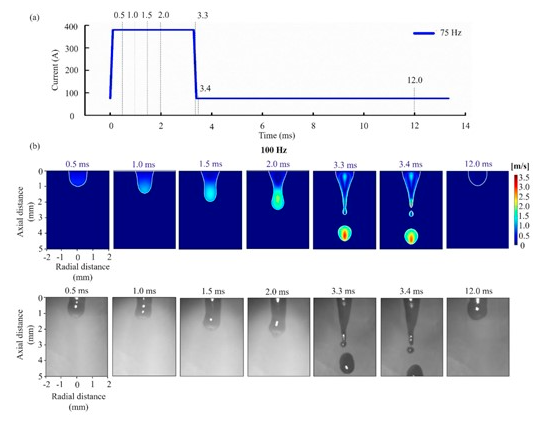
Optimizing Metal Transfer in Pulsed WAAM Through Numerical Modeling and Frequency Control
This research project focuses on the computational analysis of metal transfer modes, dynamics, and heat transfer in pulsed wire-arc additive manufacturing (WAAM) under varying pulsating frequencies. By developing a numerical model using thermomagnetohydrodynamic equations and the phase-field method, the study investigates how pulse frequency influences droplet formation, detachment, and thermal behavior during the WAAM process. The findings reveal that medium pulse frequencies (100–175 Hz) achieve the optimal one-droplet-per-pulse (ODPP) transfer mode, which minimizes defects such as residual stresses and poor surface quality. Additionally, higher frequencies reduce droplet velocity and temperature, while Joule and arc heating decrease, though sheath heating remains consistent. The validated model provides valuable insights for optimizing WAAM processes, enhancing control over metal transfer stability, and improving the quality of additive-manufactured components. This work contributes to advancing WAAM technology for large-scale industrial applications.
Optimization of WEDM Parameters for Tool Steel D2
This research project investigates the optimization of key process parameters in Wire Electrical Discharge Machining (WEDM) for tool steel D2, focusing on material removal rate (MRR), surface roughness, and kerf width. Using Taguchi’s L18 orthogonal array, the study evaluates eight control factors, including pulse on-time, open voltage, and wire tension, to determine their influence on machining performance. Statistical tools like ANOVA and signal-to-noise (S/N) ratios identify pulse on-time as the most significant parameter for all three responses. Linear regression and additive models are developed to predict outcomes, validated through confirmatory experiments with high accuracy (average errors of 1.26–2.24%). The findings provide actionable insights for achieving optimal machining conditions—minimizing surface roughness and kerf while maximizing MRR—benefiting precision tool and die manufacturing industries. This work bridges theoretical analysis with practical applications, enhancing WEDM efficiency and quality.
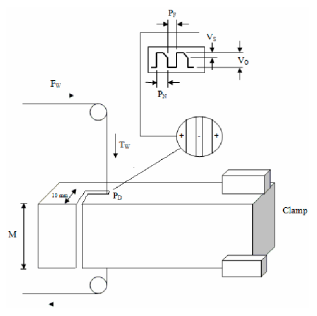
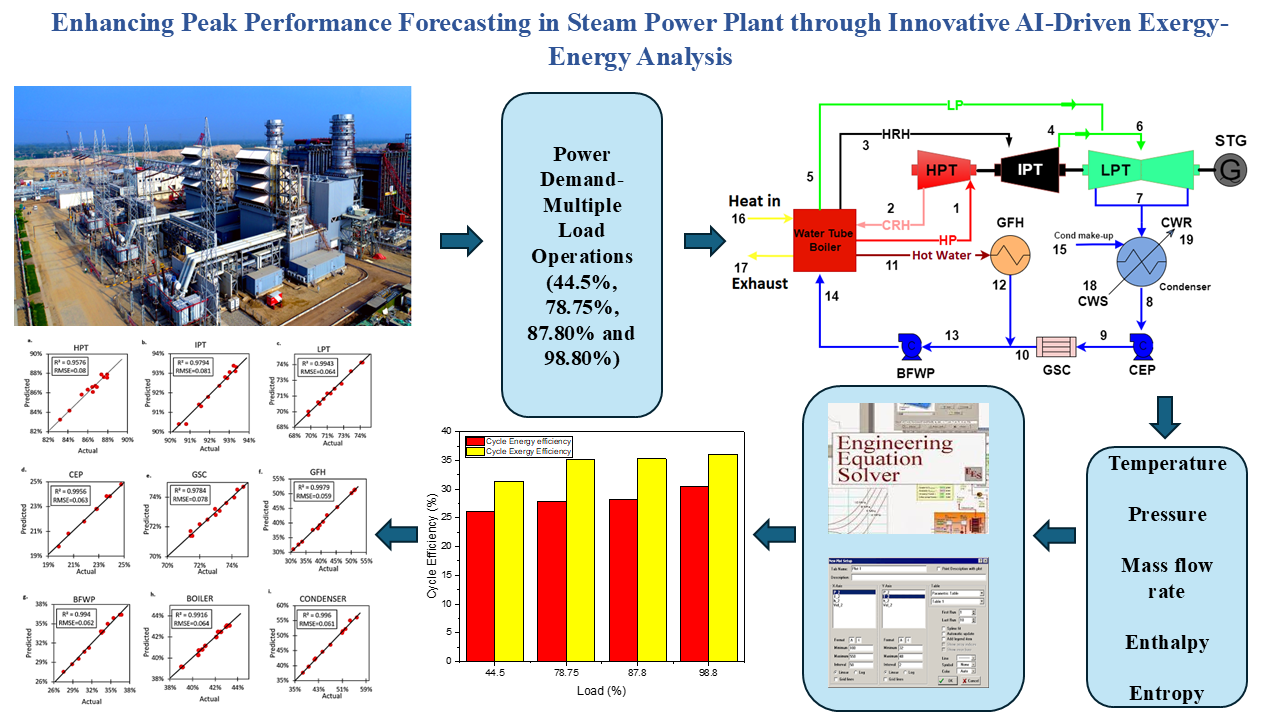
AI-Assisted Energy-Exergy Analysis for Performance Optimization of a 400 MW Steam Power Plant
This research project focuses on enhancing the performance of a 400 MW steam power plant operating on the Rankine cycle through a combined exergy-energy analysis and an innovative AI-driven random forest regression model. The study evaluates component-wise inefficiencies, identifies key parameters affecting plant performance, and develops an optimized predictive model to improve efficiency and minimize exergy losses. By integrating thermodynamic analysis with machine learning, the project highlights the boiler as the primary source of exergy destruction and demonstrates how operational adjustments, such as optimizing steam quality and reheat pressure, can significantly enhance overall plant performance. The AI model, validated with experimental data, achieves high predictive accuracy, offering a robust tool for real-time performance monitoring and optimization, ultimately contributing to more sustainable and efficient power generation.
Sustainable Biodiesel Synthesis from Waste Cooking Oil and Sesame Oil: AI-Driven Optimization and Performance Analysis
This research project focuses on optimizing biodiesel production from a blend of waste cooking oil (WCO) and sesame seed oil (SSO) using microwave-assisted transesterification, enhanced by Response Surface Methodology (RSM) and Artificial Neural Network (ANN) techniques. The study addresses the challenges of WCO’s poor cold flow properties by combining it with SSO, which offers better oxidation stability, and systematically evaluates the impact of key operational parameters—reaction speed, time, methanol-to-oil ratio, and catalyst concentration—on biodiesel yield. The ANN model outperforms RSM in predictive accuracy, achieving a maximum yield of 94% under optimized conditions (350 rpm, 3 min reaction time, 1.05% w/w catalyst, and a 10:1 methanol-to-oil ratio). The findings highlight the potential of ANN for complex nonlinear modeling in biodiesel production, offering a sustainable and efficient alternative to fossil fuels while leveraging waste resources.
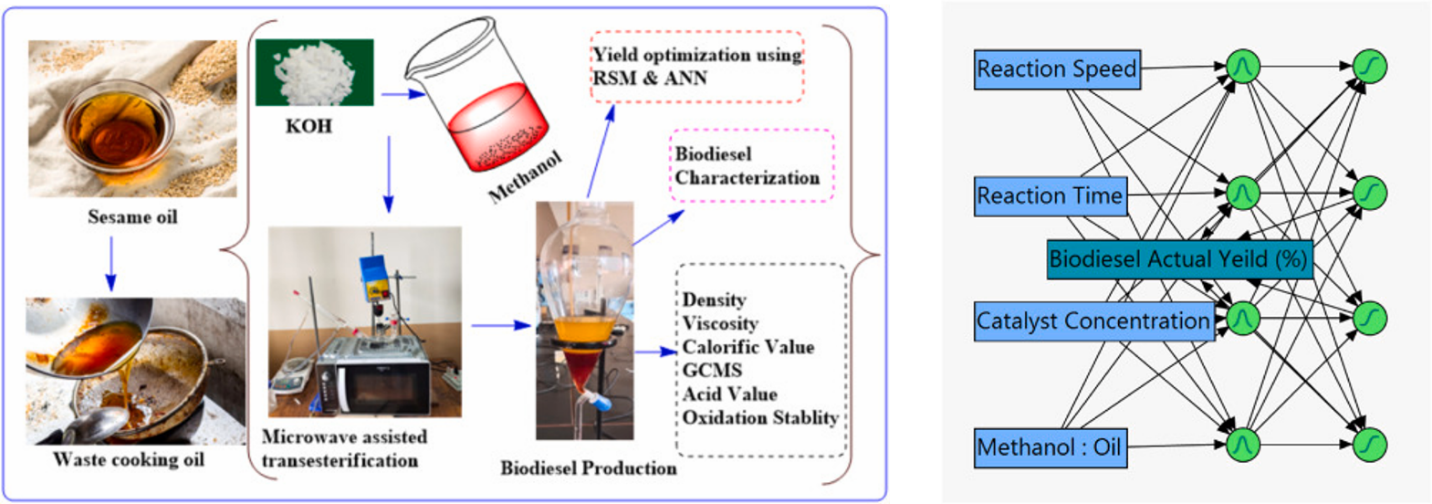
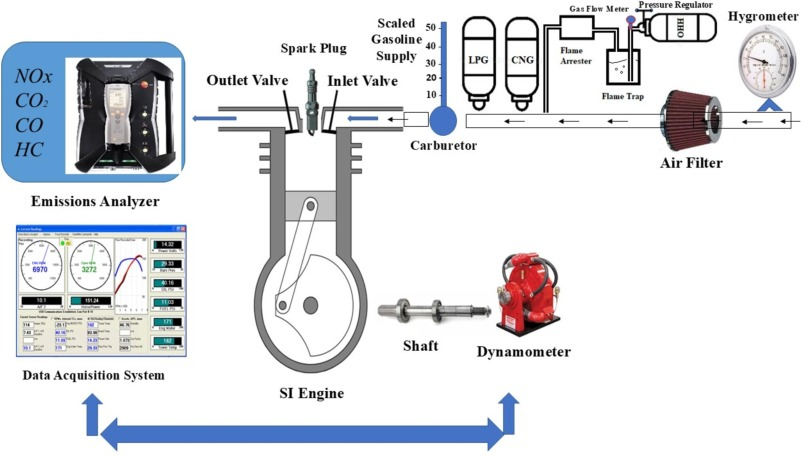
Parametric Optimization of Engine Performance and Emissions for Hydroxy Blended Gaseous Fuels
This research project explores the optimization of engine performance and emissions by blending hydroxy gas (HHO) with conventional gaseous fuels like liquefied petroleum gas (LPG) and compressed natural gas (CNG). The study addresses the power deficit of these fuels compared to gasoline by leveraging HHO’s renewable nature and superior combustion properties. Using response surface methodology (RSM) and central composite design (CCD), the project identifies optimal engine conditions, demonstrating that HHO blends significantly improve torque, brake thermal efficiency (BTE), and fuel economy while reducing harmful emissions like CO, CO₂, and HC, albeit with a slight increase in NOx. The findings highlight the potential of HHO-enriched fuels as a sustainable alternative, offering a balance between performance enhancement and environmental benefits, and underscore the efficacy of RSM in minimizing experimental costs and time. This work contributes to advancing eco-friendly fuel technologies for internal combustion engines.